Lifestyle
Obróbka metali a obróbka tworzyw sztucznych – poznajmy granice możliwości
Opublikowano
7 miesięcy temu-
Autor
Artykuł sponsorowany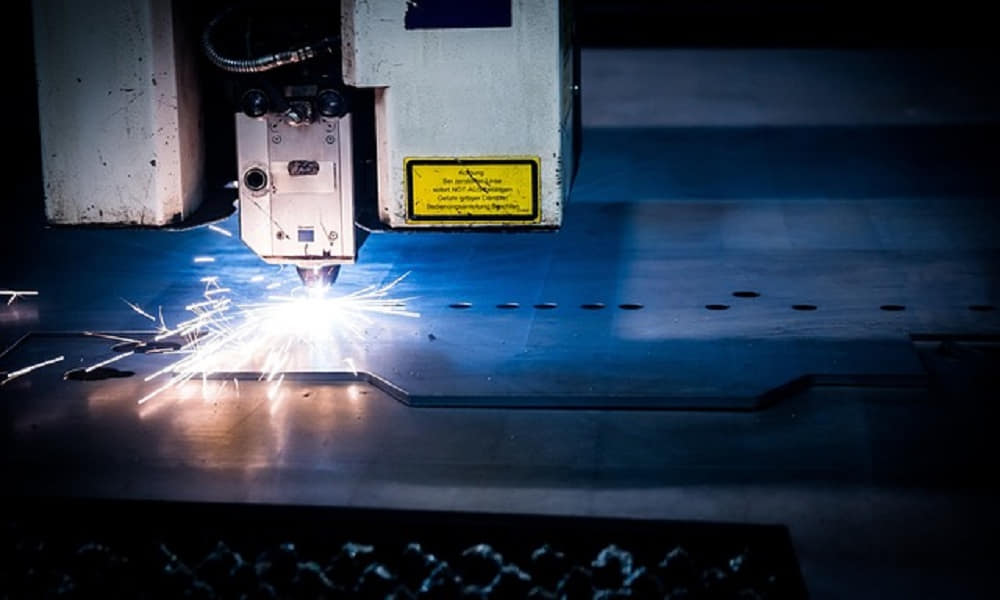
Jak myślisz, dlaczego w przemyśle jedne produkty wykonuje się ze stali z wykorzystaniem zaawansowanych maszyn CNC, a inne z polimerów przy użyciu form wtryskowych? W erze innowacyjnych technologii i nieustannej walki o lepszą wydajność produkcji wybór metody obróbki materiału może przesądzić o powodzeniu projektu, jakości wyrobu i konkurencyjności całego przedsiębiorstwa. Decyzja o tym, czy sięgnąć po metal o wysokiej wytrzymałości, czy może postawić na tworzywo sztuczne cechujące się niską masą własną, nie zależy już wyłącznie od ceny surowca. Obejmuje również analizę późniejszych kosztów eksploatacji, możliwości automatyzacji w procesie wytwarzania oraz potencjału recyklingu, a wszystko to przy zachowaniu coraz bardziej rygorystycznych norm środowiskowych. Sprawdźmy to razem.
Właściwości fizyczne metali i ich wpływ na proces wytwarzania
Metale zazwyczaj kojarzą się z wysoką gęstością, znaczną wytrzymałością i dobrym przewodnictwem cieplnym. Te cechy stanowią jednocześnie atut i wyzwanie w procesach obróbki – niezbędna jest solidna maszyna o odpowiedniej mocy, zwłaszcza gdy w grę wchodzi kucie, tłoczenie czy frezowanie. Nawet przy użyciu technologii sterowania numerycznego (CNC) trzeba brać pod uwagę wpływ wysokich temperatur powstających przy intensywnym tarciu narzędzia o metal, co może skutkować deformacjami i mikropęknięciami w nieodpowiednio chłodzonych elementach. Raport opublikowany przez Międzynarodową Organizację ds. Obróbki Skrawaniem w 2023 roku potwierdza, że błędy w doborze prędkości i głębokości skrawania powodują odchyłki wymiarowe w blisko 12% metalowych detali produkowanych masowo. Jak informuje nas Przedsiębiorstwo Produkcyjno Usługowo-Handlowe na stronie internetowej: https://kelmet.pl/, takich problemów nie można bagatelizować w przemyśle lotniczym, motoryzacyjnym czy maszynowym, gdzie powtarzalność i mikroprecyzja stanowią fundament całego łańcucha jakości.
Właściwości fizyczne tworzyw sztucznych i ich wpływ na proces obróbki
Tworzywa sztuczne różnią się natomiast niższą temperaturą topnienia, mniejszą gęstością i wrażliwością na działanie czynników chemicznych lub promieniowania UV. W efekcie do ich obróbki wystarczają lżejsze maszyny, a przy wtrysku czy termoformowaniu kluczowe jest precyzyjne zarządzanie temperaturą i ciśnieniem we wnęce formy. Zbyt wysoka temperatura może prowadzić do degradacji łańcuchów polimerowych, za niska – do niedostatecznego wypełnienia formy i powstawania porowatości. Dlatego w nowoczesnych zakładach produkcyjnych stosuje się linie wtryskowe wyposażone w zaawansowane układy pomiarowe, które w czasie rzeczywistym rejestrują rozkład temperatur i ciśnienia w kilku strefach maszyny. Dane opublikowane przez Światowe Stowarzyszenie Przetwórców Polimerów w 2022 roku pokazują, że wprowadzenie inteligentnych systemów wtryskowych umożliwia ograniczenie wad produkcyjnych o nawet 30%, zwłaszcza przy skomplikowanych kształtach detali. Mimo to należy pamiętać, że niektóre tworzywa mogą ulegać łatwej deformacji pod wpływem podwyższonej temperatury czy promieniowania słonecznego, co ogranicza ich zastosowanie w środowiskach ekstremalnie gorących lub narażonych na długotrwałą ekspozycję UV.
Zakres metod obróbki metali oraz tworzyw sztucznych
Przy obróbce metali dominującą rolę odgrywają operacje skrawania, spawania, tłoczenia, walcowania czy obróbki cieplnej. Każda z nich wymaga innego zestawu maszyn i odmiennego zaplecza inżynieryjnego, dlatego duże zakłady metalurgiczne inwestują w rozbudowane linie produkcyjne zintegrowane z systemami sterowania numerycznego. W opinii specjalistów, automatyzacja tych procesów pozwala zwiększyć wydajność o 25–40%, ograniczając udział czynnika ludzkiego w najbardziej powtarzalnych zadaniach. Z kolei w przypadku tworzyw sztucznych najważniejsze znaczenie ma technologia wtrysku, termoformowania i w mniejszym stopniu skrawania (choć wciąż jest ono spotykane np. przy prototypach). Nowoczesne wtryskarki wyposażone w roboty manipulacyjne umożliwiają przejęcie detalu bezpośrednio po wyformowaniu, przeniesienie go do systemu chłodzenia i wykonanie wstępnej inspekcji jakości. Według raportu Europejskiego Komitetu ds. Automatyzacji z 2024 roku, przedsiębiorstwa produkcyjne, które zintegrowały linie wtryskowe z robotyką, zredukowały liczbę braków o średnio 18% w ciągu pierwszych dwunastu miesięcy od wdrożenia. Trzeba jednak podkreślić, że nie każde tworzywo jest równie podatne na automatyzację – niektóre zaawansowane polimery wymagają specyficznych warunków przetwórczych, co przekłada się na koszty i skomplikowanie całej instalacji.
Koszty produkcji w obróbce metali i tworzyw sztucznych
Aspekt finansowy stanowi jeden z głównych wyznaczników wyboru technologii i materiału. Obróbka metali, zwłaszcza tych o podwyższonej twardości, wymaga stosowania frezów i wierteł wykonanych z węglików spiekanych lub diamentowych, co wpływa na wysokie ceny narzędzi. Dodatkowo maszyny do skrawania z dużymi prędkościami obrotowymi są kosztowne w zakupie i utrzymaniu, ale znacząco skracają czas produkcji. W przemyśle form wtryskowych, gdzie głównym surowcem są polimery, koszty wytwarzania rozkładają się głównie na zakup granulatów oraz zaprojektowanie skomplikowanych form stalowych, które potrafią pracować w trybie wielkoseryjnym bez istotnego zużycia. Formy wtryskowe należą jednak do najbardziej wymagających elementów produkcyjnych – ich projektowanie zajmuje wiele tygodni, a błędne wymiarowanie może podnieść koszty aż o kilkadziesiąt procent, uwzględniając późniejsze korekty. Z danych opublikowanych przez Międzynarodową Federację Przemysłu Tworzyw Sztucznych w 2023 roku wynika, że formy wtryskowe stanowią nawet 40% całkowitego budżetu uruchomienia nowej linii produkcyjnej, jednak w dużych wolumenach wytwarzania potrafią przełożyć się na istotne oszczędności jednostkowe.
Warto zauważyć, że ekonomia skali działa korzystnie w obu przypadkach. Przy masowej obróbce stali z użyciem zautomatyzowanych frezarek i tokarek można osiągnąć niskie koszty jednostkowe, o ile wolumen zamówień jest wystarczająco duży. Analogicznie, tworzywa sztuczne wtryskiwane masowo przy optymalnie ustawionych parametrach pozwalają na szybkie i tanie wytworzenie tysięcy identycznych detali dziennie. W sytuacjach prototypowych czy niskoseryjnych różnice bywają jednak uderzające. Metal można bowiem stosunkowo łatwo obrabiać metodami uniwersalnymi (skrawanie, wycinanie laserem) bez konieczności posiadania specjalistycznej formy, podczas gdy w przypadku tworzyw sztucznych już samo wykonanie formy wtryskowej generuje duże koszty, co przy małej liczbie sztuk może okazać się nieopłacalne.
Trwałość, recykling i ekologia
W dobie rosnącej świadomości ekologicznej obróbka materiałów musi uwzględniać wpływ na środowisko naturalne. Metale są surowcem, który można w większości recyklingować, przetapiając zużyte komponenty na nowy surowiec i ograniczając wydobycie rud w kopalniach. Proces ten bywa jednak energochłonny, a emisja dwutlenku węgla związana z pracą hut pozostaje wysoką barierą do pokonania dla sektora metalurgicznego. Według statystyk Światowej Rady ds. Emisji z 2022 roku, produkcja jednej tony stali generuje średnio 1,8 tony CO₂, choć najnowocześniejsze huty potrafią obniżyć ten wskaźnik nawet o 15–20%. Tworzywa sztuczne z kolei w trakcie wytwarzania mogą powodować mniejszą emisję gazów cieplarnianych, ale ich recykling jest uzależniony od rodzaju polimeru i dostępności infrastruktury selektywnej zbiórki odpadów. Wiele zaawansowanych tworzyw inżynieryjnych, stosowanych np. w branży samochodowej czy AGD, zawiera liczne domieszki chemiczne utrudniające ponowne przetwarzanie, co przekłada się na wysoki poziom odpadów niesegregowanych. Instytut Badań nad Recyklingiem podaje, że w Unii Europejskiej jedynie około 30% ogółu tworzyw sztucznych poddaje się efektywnemu recyklingowi, podczas gdy 70% trafia do spalarni lub składowisk.
Odpady produkcyjne powstałe podczas obróbki
Oprócz samego zużycia energii ważne są też odpady produkcyjne. Przy frezowaniu lub toczeniu metali powstają skrawki i wióry, które można sprzedać do firm zajmujących się recyklingiem, z kolei w przypadku wtrysku tworzyw sztucznych niekiedy występują nadlewki, z których część da się przetopić i wykorzystać ponownie. Innowacyjne zakłady wdrażają rozwiązania takie jak systemy do gromadzenia i regranulacji tworzywa w trakcie procesu, ograniczając straty materiałowe nawet o 60%. Coraz częściej pojawiają się też kompozyty o biodegradowalnych matrycach polimerowych, jednak wciąż pozostają one w fazie rozwoju i nie zawsze spełniają wymagania techniczne stawiane przez branże high-tech.
Przyszłe kierunki rozwoju i trendy w przetwórstwie
W świetle dynamicznych zmian technologicznych oraz rosnących oczekiwań rynku, obróbka metali i tworzyw sztucznych stopniowo się przenikają, doprowadzając do powstawania materiałów hybrydowych, łączących najlepsze cechy obu światów. Nowe stopy aluminium o wysokiej wytrzymałości i odporności na korozję konkurują z polimerami zbrojonymi włóknem węglowym o porównywalnej charakterystyce. Zespoły badawcze pracują nad drukiem 3D metali i tworzyw, co otwiera potencjał projektowania kształtów niemożliwych do uzyskania tradycyjnymi metodami. Według analityków z Międzynarodowego Centrum Rozwoju Przemysłu 4.0, do 2030 roku aż 20% wyrobów przemysłowych może pochodzić z procesów addytywnych, bazujących na warstwowym nakładaniu proszków lub filamentów. Tego typu technologie będą wymagały szerokiej wiedzy o złożonych reakcjach termicznych i mechanicznych zarówno w obrębie metalowych stopów, jak i kompozytów polimerowych. Wszystkie te zmiany, związane z rozwojem automatyki, robotyki i oprogramowania projektowego, sprawiają, że jedną z najważniejszych umiejętności w przemyśle stanie się elastyczność – zdolność szybkiego dostosowania procesu i materiału do konkretnych wymagań, by w finalnym wyrobie zaistniała równowaga pomiędzy kosztem, funkcjonalnością i oddziaływaniem na środowisko.
Nowe technologie pozwalają przekraczać granice tradycyjnych podziałów między obróbką metali a przetwarzaniem tworzyw sztucznych, otwierając drogę do materiałów hybrydowych i inteligentnych procesów produkcyjnych. W efekcie przemysł osiąga coraz większą swobodę w tworzeniu wyrobów idealnie dopasowanych do wymagań rynku, odciążając przy tym środowisko naturalne.
Podróże
Weekend w górach – dlaczego Karpacz to najlepszy wybór na krótki wypoczynek?
Opublikowano
6 dni temu-
27 sierpnia 2025Autor
Artykuł sponsorowany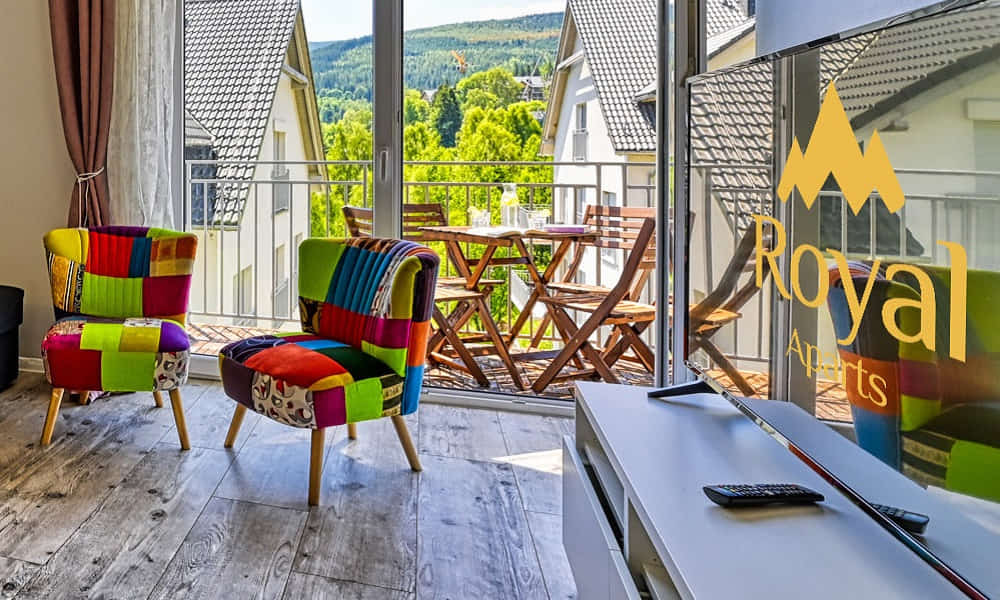
Krótki wyjazd w góry to doskonały sposób, by oderwać się od codzienności i zregenerować siły. W Polsce jednym z najlepszych kierunków na weekendowy wypoczynek jest Karpacz – miasto, które łączy piękne widoki, bogactwo atrakcji i komfortowe noclegi. Dzięki ofercie Royal Aparts Karpacz możesz cieszyć się nie tylko przestronnymi apartamentami, ale także opcjami pobytu ze śniadaniem czy pełnym wyżywieniem i basenem. (więcej…)
Lifestyle
Czy pilates może poprawić jakość snu?
Opublikowano
2 tygodnie temu-
21 sierpnia 2025Autor
Artykuł partnera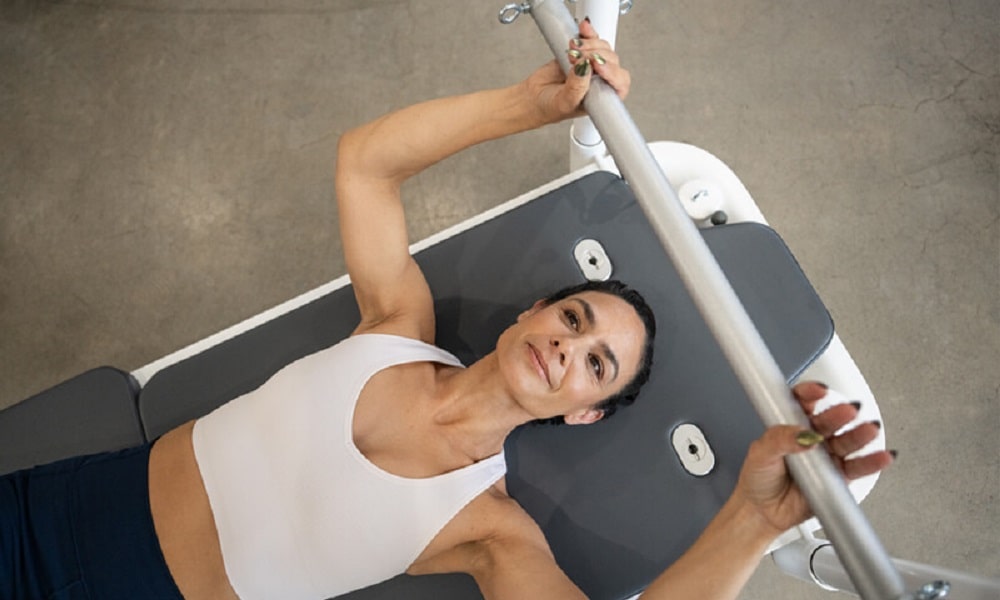
Sen nie jest luksusem – to biologiczna konieczność. W czasie snu zachodzi regeneracja układu nerwowego, odbudowa mięśni i regulacja hormonalna. Jakość nocnego wypoczynku wpływa na naszą odporność, nastrój, koncentrację, metabolizm, a nawet wagę. Problem pojawia się, gdy sen staje się przerywany, zbyt krótki lub trudny do osiągnięcia. Współczesny tryb życia – ekranizacja, stres, nieregularność – pogarsza parametry snu u coraz większej liczby osób. (więcej…)
Lifestyle
Jak przygotować się na pierwsze zajęcia pilates?
Opublikowano
2 tygodnie temu-
21 sierpnia 2025Autor
Artykuł partnera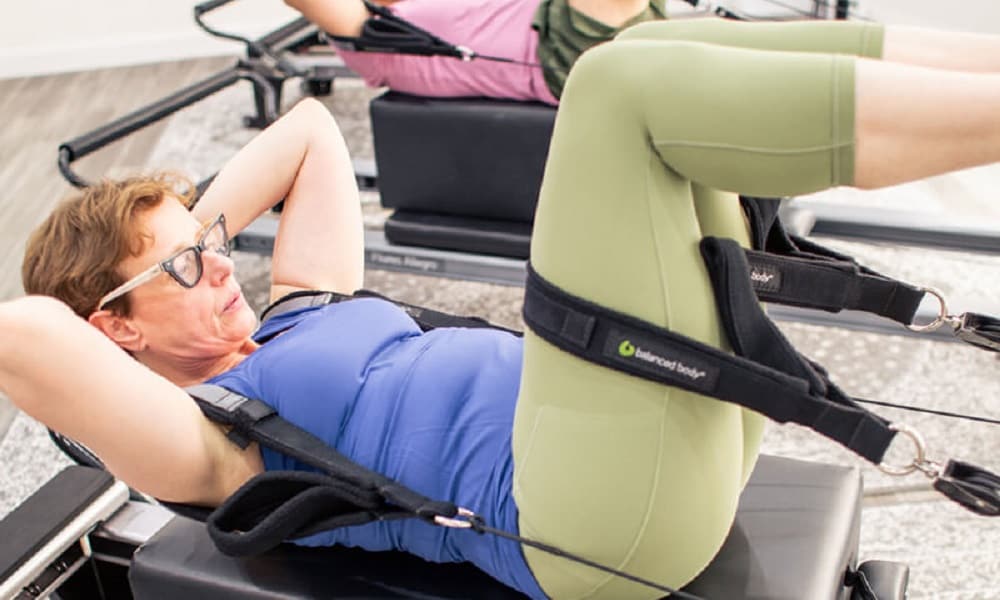
Pierwszy krok zawsze wydaje się najtrudniejszy. Zwłaszcza jeśli wchodzisz na salę, gdzie inni już wiedzą, jak oddychać, jak ułożyć miednicę, jak aktywować centrum. Ale pilates to nie pokaz umiejętności – to podróż, która zaczyna się od Ciebie, takiej, jaka jesteś dziś. Nie musisz być silna, elastyczna ani znać nazw mięśni głębokich. Wystarczy, że przyjdziesz. (więcej…)
Lifestyle
Jak często ćwiczyć pilates, żeby zobaczyć efekty?
Opublikowano
2 tygodnie temu-
21 sierpnia 2025Autor
Artykuł partnera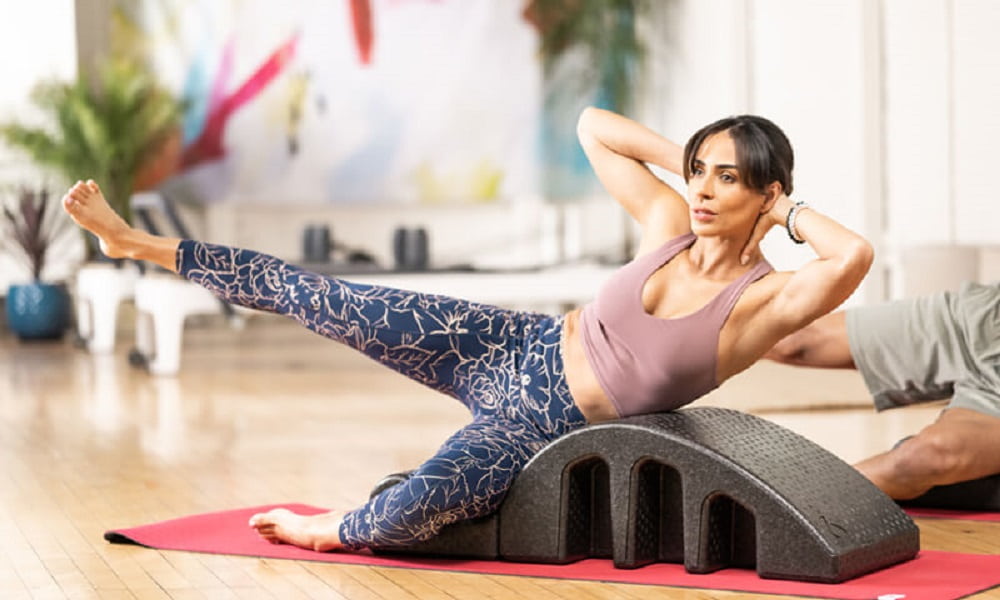
Pilates nie daje natychmiastowych rezultatów, ale daje trwałą zmianę – pod warunkiem, że ćwiczysz regularnie. W świecie pełnym obietnic szybkich metamorfoz, metoda oparta na precyzji, cierpliwości i świadomym ruchu może wydawać się zbyt subtelna, by była skuteczna. A jednak to właśnie w tej subtelności tkwi jej siła. Jeśli zastanawiasz się, jak często trzeba ćwiczyć pilates, by zobaczyć pierwsze efekty – nie tylko w sylwetce, ale też w samopoczuciu, postawie i odczuwaniu własnego ciała – odpowiedź nie jest tak oczywista, jak mogłoby się wydawać. (więcej…)
Lifestyle
Łóżko na pilota dla chorych – jak z niego korzystać?
Opublikowano
2 tygodnie temu-
21 sierpnia 2025Autor
Artykuł partnera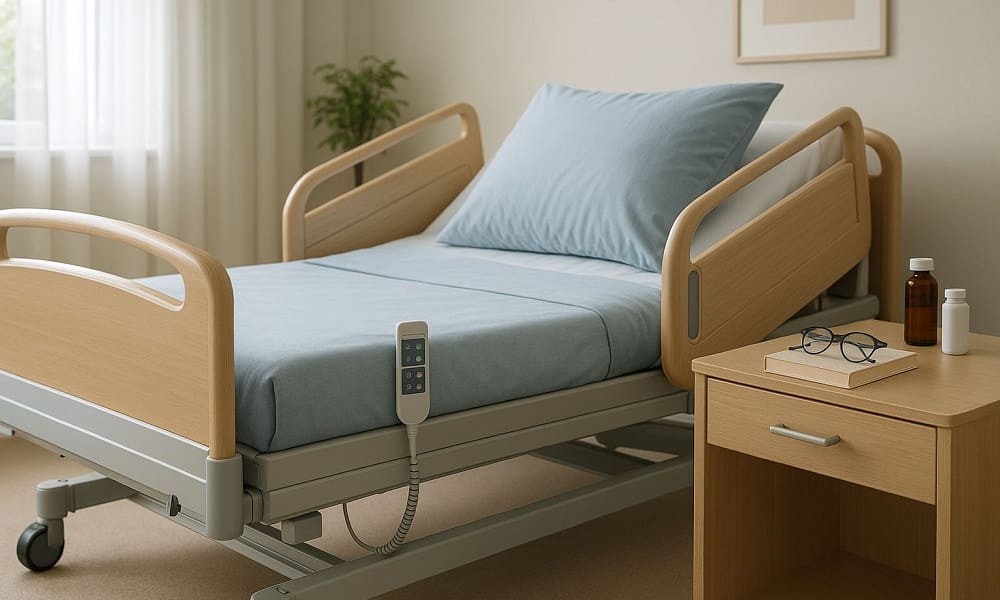
Opieka nad osobą leżącą lub z ograniczoną mobilnością to codzienne balansowanie między komfortem pacjenta a bezpieczeństwem pracy opiekuna. W tym zadaniu nieocenioną pomocą jest łóżko rehabilitacyjne z napędem elektrycznym, które potrafi całkowicie odmienić jakość życia obu stron. Jednak nawet najlepszy model nie przyniesie pełnych korzyści, jeśli jego funkcje będą wykorzystywane w sposób przypadkowy lub niewłaściwy. Kluczowym elementem obsługi jest pilot sterujący – mały, ale niezwykle istotny kontroler, który jednym przyciskiem potrafi zmienić ułożenie ciała pacjenta, odciążyć określone partie mięśni i stawów czy poprawić krążenie. W tym poradniku podpowiadam, jak korzystać z pilota świadomie i efektywnie, aby stał się nie tylko narzędziem wygody, ale też elementem codziennej terapii. (więcej…)
Lifestyle
Jak dbać o higienę skóry osoby długotrwale leżącej?
Opublikowano
2 tygodnie temu-
21 sierpnia 2025Autor
Artykuł partnera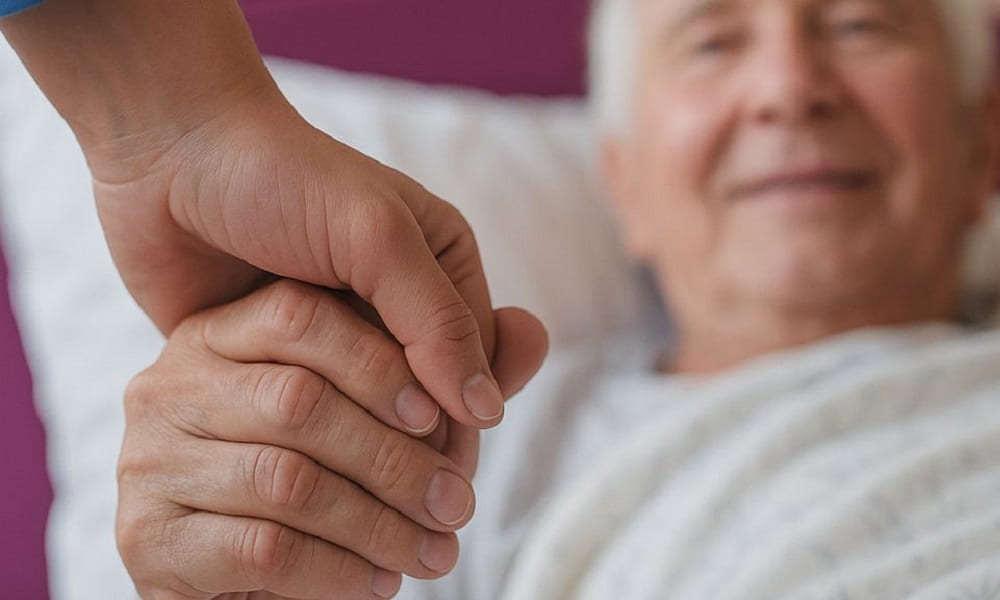
Długotrwałe unieruchomienie w łóżku to ogromne wyzwanie nie tylko dla układu ruchu czy krążenia, ale także dla skóry pacjenta. Brak zmiany pozycji, ucisk ciała na podłoże i ograniczony dostęp do świeżego powietrza zwiększają ryzyko odleżyn, podrażnień, stanów zapalnych czy grzybic. Skóra staje się delikatniejsza, cieńsza i podatna na uszkodzenia. Dlatego pielęgnacja nie może ograniczać się do mycia – to codzienny proces profilaktyki, nawilżania i ochrony, który decyduje o komforcie i zdrowiu chorego. (więcej…)
Najnowsze informacje
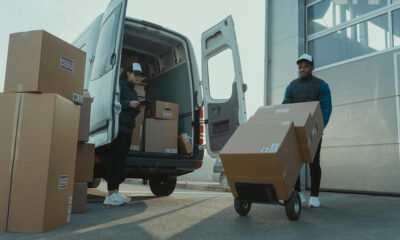

Materiały, które pracują razem z Tobą – dlaczego warto wybrać sprawdzone rozwiązania?
W każdej firmie liczy się jakość i niezawodność – niezależnie od tego, czy działasz w logistyce, budownictwie, usługach serwisowych czy zarządzasz zapleczem produkcyjnym. W natłoku codziennych obowiązków...
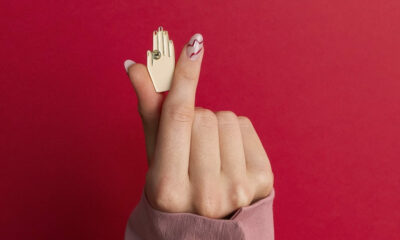

Kolekcjonerskie piny Rossmann x Kopi
W Rossmannie już od 30 lipca do zdobycia kolekcjonerskie piny zaprojektowane przez Natalię Kopiszkę. Zdobędziesz je wykonując zadania czekające w aplikacji Rossmann PL. Podejmij się misji, odwiedź...
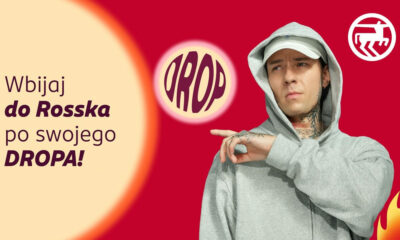

„Wbijaj do Rosska po swojego dropa” – nowa kampania Rossmanna
W drogeriach Rossmann wylądował właśnie kolejny kosmetyczny drop. Tym razem są to limitowane produkty do makijażu od Everybody London. Razem z nim wystartowała nowa kampania. Jej...
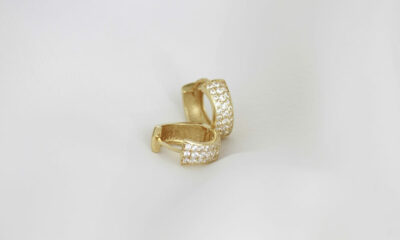

Złote kolczyki – ponadczasowy wybór dla każdej kobiety
Złote kolczyki to jeden z tych elementów biżuterii, który od pokoleń pozostaje symbolem elegancji, klasy i dobrego smaku. Ich uniwersalny charakter sprawia, że doskonale komponują się...
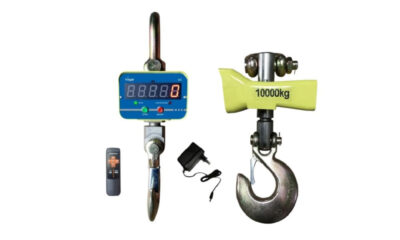

Inwestycja w dokładność, czyli właściwy wybór urządzeń ważących, zwraca się w przypadku małych i średnich przedsiębiorstw
W dzisiejszym biznesie dokładność jest kluczem do sukcesu. W przypadku małych i średnich przedsiębiorstw marża jest często niewielka.
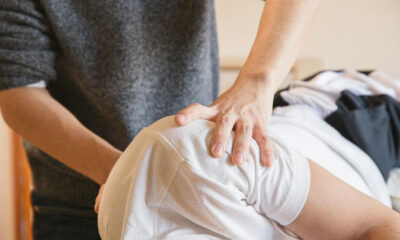

Kiedy udać się do fizjoterapeuty? Objawy, których nie można ignorować
Masz ból pleców, ograniczoną ruchomość lub przewlekłe napięcie mięśni? Sprawdź, kiedy warto udać się do fizjoterapeuty i jakie objawy powinny Cię zaniepokoić.
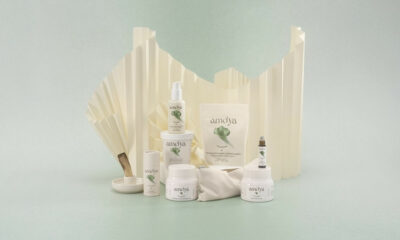

Rossmann: Z Amo’ya bądź dla siebie codziennie
Już jest – nowa, wyjątkowa marka, dostępna tylko w drogeriach Rossmann. Zachęca do traktowania swojego ciała z uwagą i czułością, do „bycia dla siebie codziennie”.
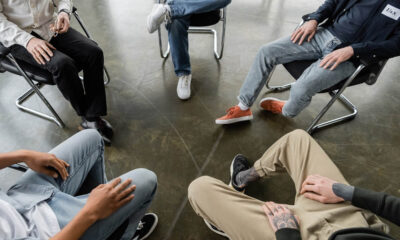

Jak działa ośrodek leczenia uzależnień w Kielcach? Przebieg terapii
Nosisz się z zamiarem podjęcia terapii uzależnień? A może członek Twojej najbliższej rodziny zmaga się z nałogiem i chcesz mu pomóc? Wybierz dobry ośrodek leczenia uzależnień,...


Nadzieje Kielc 2025 przyznane. Zobacz do kogo trafiły nagrody
Za nami jubileuszowa, 30. edycja gali „Nadzieje Kielc”. To wyróżnienie dla młodych ludzi z pasją, ambicją i imponującymi osiągnięciami – w nauce, kulturze, sporcie i działalności...
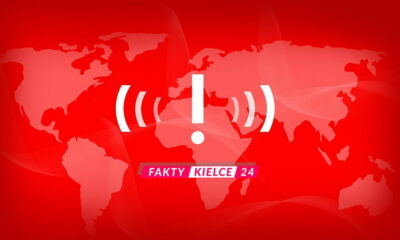

Pacjent zaatakował pielęgniarza w kieleckim szpitalu. Poważne złamanie ręki
Agresywny incydent na SOR-ze
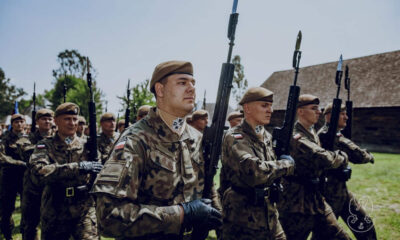

Świętokrzyska Brygada Obrony Terytorialnej świętowała 7. rocznicę powstania
10 Świętokrzyska Brygada Obrony Terytorialnej (10 ŚBOT) po raz siódmy obchodziła swoje święto. Główne uroczystości odbyły się 10 czerwca w Parku Etnograficznym...
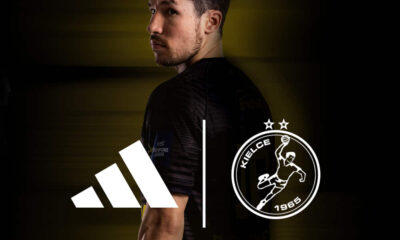

Industria Kielce z nowym partnerem. Od sezonu 2025/2026 w strojach adidas
Legenda polskiej piłki ręcznej łączy siły z adidas
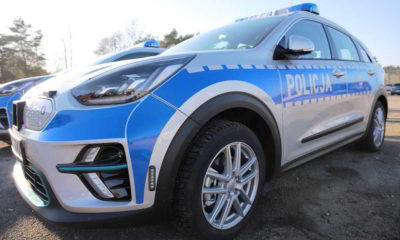

Policja zlikwidowała plantację marihuany – zabezpieczono 2 kg suszu i 28 krzewów
Nielegalna uprawa konopi odkryta przez policję
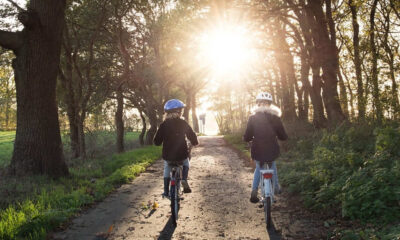

Kazimierza Wielka z nową trasą rowerową! Są pieniądze na projekt „Rowerowe SPA VELO”
Świętokrzyskie inwestuje w turystykę rowerową – w latach 2025-2027 powstanie nowy odcinek ścieżki rowerowej w Kazimierzy Wielkiej, który połączy uzdrowiskowe atrakcje regionu.
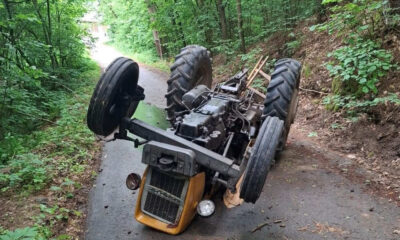

Świętokrzyskie: 81-latek przygnieciony przez własny ciągnik [zdjęcia]
Do groźnego wypadku doszło w sobotę (7.06) na leśnym odcinku ul. Trójca w Zawichoście. 81-letni rolnik został przygnieciony przez wywrócony ciągnik Ursus, ale samodzielnie wydostał się spod...
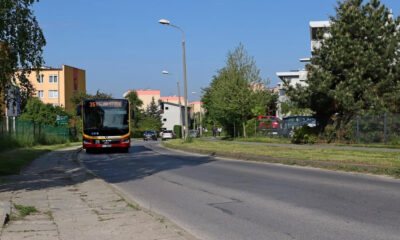

Kielce szykują się do remontów ulic Piekoszowskiej i Kołłątaja
Miejski Zarząd Dróg wkrótce wybierze wykonawców prac, które mają poprawić stan nawierzchni dwóch ważnych arterii w mieście. Prace potrwają 120 dni...
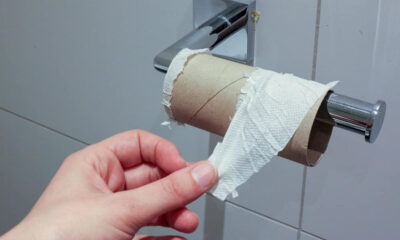

Świętokrzyskie: Wycieczka zostawiła dziecko w toalecie restauracji… i odjechała
Szokujące zdarzenie w Sandomierzu: grupa wycieczkowa odjechała, zostawiając w toalecie pizzerii 7-letniego chłopca. Dzięki czujności właściciela lokalu dziecko zostało odnalezione, ale sytuacja budzi...
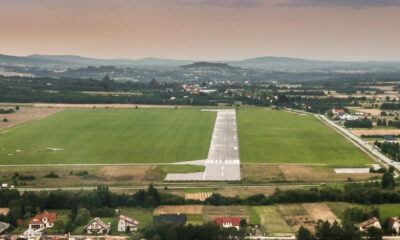

Radni Masłowa blokują utworzenie Centrum Historii Lotnictwa. „Jest wiele ważniejszych inwestycji…”
Po burzliwej sześciogodzinnej debacie radni gminy Masłów nie wyrazili zgody na zmianę wieloletniej prognozy finansowej, blokując budowę Centrum Historii Lotnictwa, nowej atrakcji regionu.
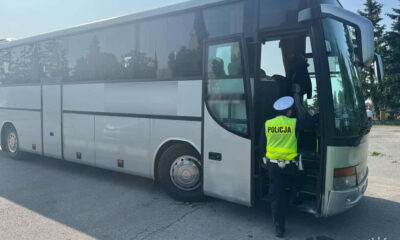

Kierowca zignorował zakaz jazdy i wiózł dzieci autokarem z pękniętą szybą! Interwencja policji w Sandomierzu
Policjanci z Sandomierza udaremnili niebezpieczny wyjazd 20 uczniów na wycieczkę szkolną. Kierowca autokaru, mimo wcześniejszego zakazu, zdecydował się jechać niesprawnym pojazdem.
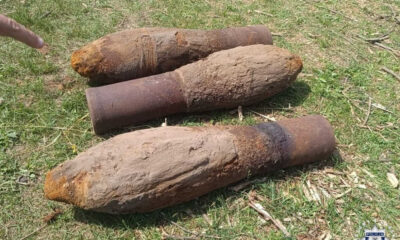

Świętokrzyskie: Niewybuch w… podporach szopy
Podczas prac porządkowych na prywatnej posesji w Ludwinowie (gm. Małogoszcz) 46-letni mężczyzna odkrył cztery rakiety kalibru 210 mm pochodzące z czasów II Wojny Światowej....
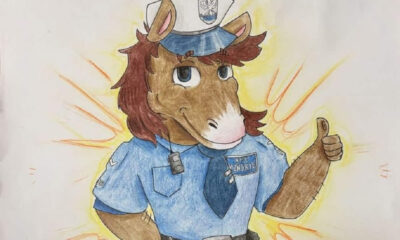

Policja z Końskich ma swoją maskotkę. To Sierżant Kuc
Ponad 300 prac konkursowych, mnóstwo kreatywności i w końcu – zwycięzcy! Komenda Powiatowa Policji w Końskich ma już swoją oficjalną maskotkę, która będzie towarzyszyć funkcjonariuszom...
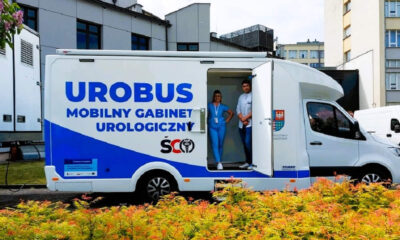

Urobus w Świętokrzyskiem: Bezpłatne badania urologiczne dla mężczyzn 45+
Mobilna pracownia urologiczna jeździ po regionie, oferując darmowe badania profilaktyczne. To szansa na wczesne wykrycie nowotworów i innych chorób układu moczowo-płciowego!
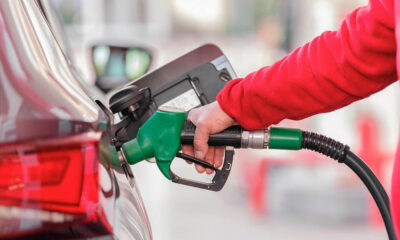

Skąd bierze się paliwo na kieleckich stacjach? Zajrzyj za kulisy logistyki Orlenu, BP i Shell
Czy zastanawiałeś się kiedyś, skąd pochodzi paliwo, które tankujesz na co dzień? Choć może się wydawać, że każda stacja dostaje paliwo prosto z rafinerii, rzeczywistość...
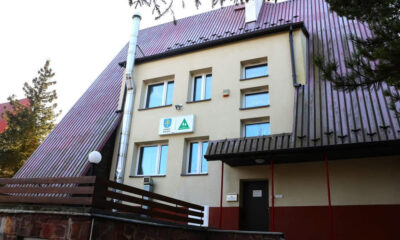

Schroniska młodzieżowe w Górach Świętokrzyskich – idealna baza dla turystów
Planujesz aktywny wypoczynek w regionie świętokrzyskim? Sprawdź ofertę komfortowych i niedrogich schronisk w Mąchocicach i Chęcinach!
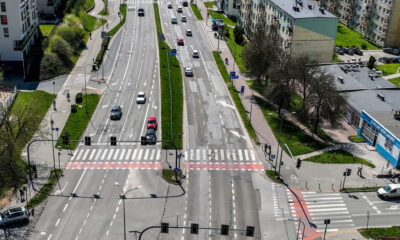

Remont ul. Warszawskiej w Kielcach rusza już wkrótce! Co się zmieni i jakich utrudnień się spodziewać?
Miejski Zarząd Dróg w Kielcach podpisał umowę na remont nakładkowy ul. Warszawskiej. Prace potrwają 120 dni i obejmą odcinek od ul. Turystycznej do ul. Jesionowej. Kierowcy zyskają nową,...
Z kraju i ze świata
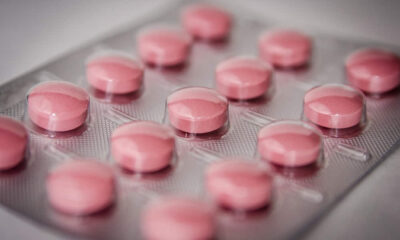

Samoleczenie w Polsce: 55% obywateli radzi sobie z drobnymi dolegliwościami bez wizyty u lekarza
Polska jest liderem w UE pod względem samoleczenia – aż 55% pacjentów samodzielnie radzi sobie z łagodnymi objawami. Eksperci podkreślają, że odpowiedzialne samoleczenie odciąża system...
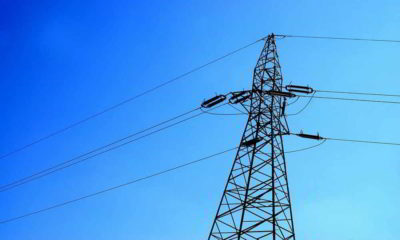

Polsce zabrakło mocy! Awaryjna dostawa prądu zza granicy! Czy grożą nam blackouty?
Poniedziałkowy wieczór (2 czerwca) przyniósł niepokojące sygnały – polski system energetyczny był na skraju wydolności. Słońce zaszło, wiatr ucichł, a elektrownie nie nadążały...
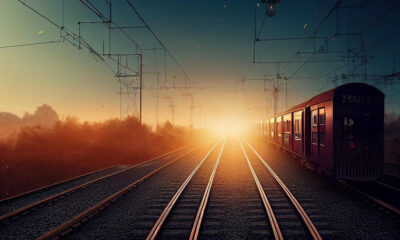

Rekordowy spadek ograniczeń prędkości na polskich kolejach. Pociągi punktualniejsze niż kiedykolwiek
Liczba ograniczeń na polskiej sieci kolejowej drastycznie spadła w ostatnich latach. W 2024 r. Polskie Linie Kolejowe S.A. odnotowały historyczny, 27-procentowy spadek, a do maja 2025 r....
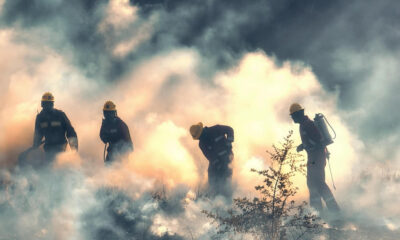

Kanada w ogniu. Największa ewakuacja w historii – prawie 100 pożarów wymknęło się spod kontroli
Ponad 17 tysięcy osób ewakuowanych, setki pożarów i dramatyczna walka z żywiołem – Kanada mierzy się z jednym z najpoważniejszych kryzysów w swojej historii. Władze ostrzegają...
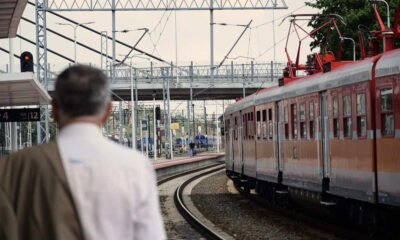

Wakacyjne zmiany na kolei: nowe przystanki, krótsze czasy przejazdów
Od 15 czerwca podróżowanie pociągami stanie się szybsze i wygodniejsze. Wprowadzana korekta rozkładu jazdy przyniesie wiele zmian, w tym nowe przystanki, skrócone czasy...
Przeczytaj też
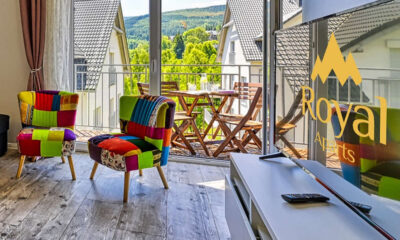

Weekend w górach – dlaczego Karpacz to najlepszy wybór na krótki wypoczynek?
Krótki wyjazd w góry to doskonały sposób, by oderwać się od codzienności i zregenerować siły. W Polsce jednym z najlepszych kierunków na weekendowy wypoczynek jest Karpacz – miasto,...
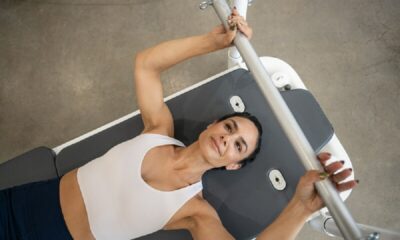

Czy pilates może poprawić jakość snu?
Sen nie jest luksusem – to biologiczna konieczność. W czasie snu zachodzi regeneracja układu nerwowego, odbudowa mięśni i regulacja hormonalna. Jakość nocnego wypoczynku wpływa...
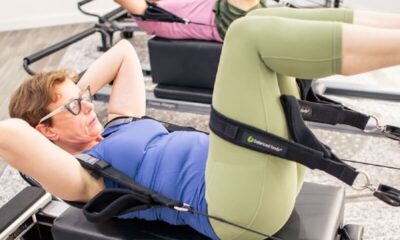

Jak przygotować się na pierwsze zajęcia pilates?
Pierwszy krok zawsze wydaje się najtrudniejszy. Zwłaszcza jeśli wchodzisz na salę, gdzie inni już wiedzą, jak oddychać, jak ułożyć miednicę, jak...
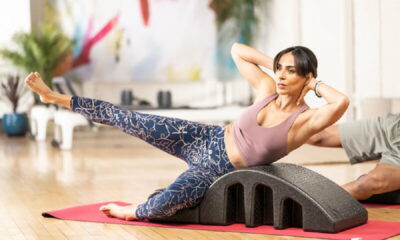

Jak często ćwiczyć pilates, żeby zobaczyć efekty?
Pilates nie daje natychmiastowych rezultatów, ale daje trwałą zmianę – pod warunkiem, że ćwiczysz regularnie. W świecie pełnym obietnic szybkich metamorfoz, metoda oparta na precyzji, cierpliwości...
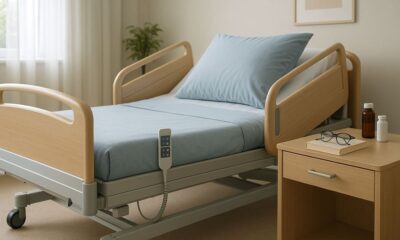

Łóżko na pilota dla chorych – jak z niego korzystać?
Opieka nad osobą leżącą lub z ograniczoną mobilnością to codzienne balansowanie między komfortem pacjenta a bezpieczeństwem pracy opiekuna. W tym zadaniu nieocenioną pomocą jest łóżko...
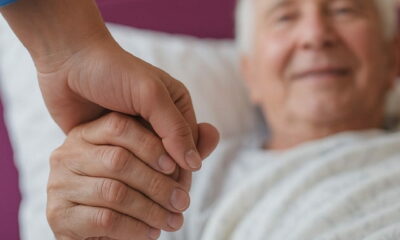

Jak dbać o higienę skóry osoby długotrwale leżącej?
Długotrwałe unieruchomienie w łóżku to ogromne wyzwanie nie tylko dla układu ruchu czy krążenia, ale także dla skóry pacjenta. Brak zmiany pozycji, ucisk ciała na podłoże i ograniczony dostęp...
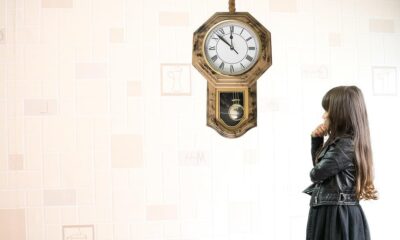

Jak nauczyć dziecko zegara? 14 sprawdzonych metod
Poznawanie zegara staje się fascynującą przygodą, gdy kolejne etapy wprowadzamy w rytmie dziecięcych zabaw. Od rozróżniania pór dnia, przez własnoręcznie zbudowaną tarczę, aż po pierwsze wyzwania...
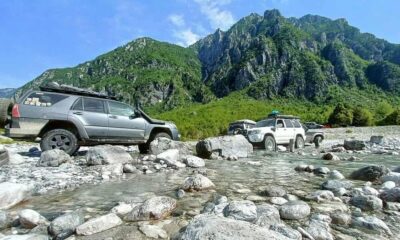

Wyprawa terenówką po bezdrożach
W dzisiejszych czasach coraz więcej osób marzy o prawdziwej przygodzie z dala od utartych szlaków. Wyprawa wynajętą terenówką na zorganizowaną wyprawę turystyczną po odległych bezdrożach to idealny...
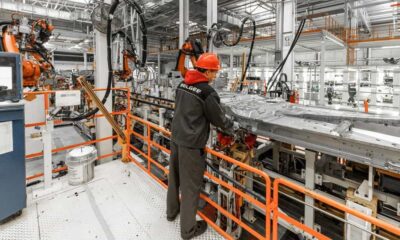

Blachy stalowe niskostopowe – fakty i ciekawostki
Blachy stalowe niskostopowe stanowią jedną z najpowszechniej stosowanych form stali w przemyśle. Ich produkcja opiera się na procesach walcowania, które mogą być prowadzone...
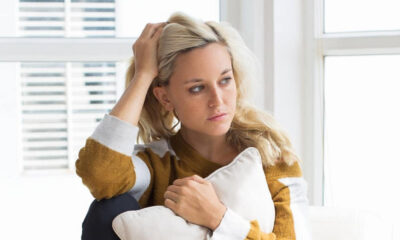

Zdrowie psychiczne a hormony – jak badania mogą pomóc, gdy brakuje Ci energii i nastroju?
Spadek nastroju, brak energii, rozdrażnienie i trudności ze snem to dolegliwości, które wielu z nas zna aż za dobrze. Często tłumaczymy je przemęczeniem, „gorszym okresem” albo pogodą. Tymczasem...
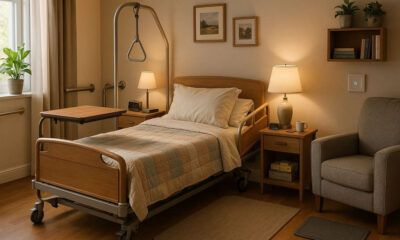

5 elementów, bez których komfortowa opieka domowa się nie uda
Domowa opieka nad osobą chorą, leżącą lub z niepełnosprawnością to ogromne wyzwanie. To codzienność pełna obowiązków, stresu i decyzji, które bez odpowiedniego wsparcia mogą przerodzić się...


Jak zapobiegać wilgoci i pleśni w domu?
Wilgoć i pleśń w domu to nie tylko problem estetyczny, ale także poważne zagrożenie dla zdrowia domowników i trwałości budynku. Grzyb pojawiający się na ścianach może powodować alergie,...
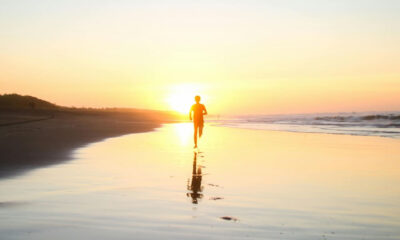

Bieganie w pełnym słońcu. Na co uważać, żeby nie przesadzić?
Bieganie w środku dnia, kiedy słońce praży jak opiekacz do tostów, może być zarówno błogim resetem, jak i przepisem na zjazd energetyczny rodem z filmu...
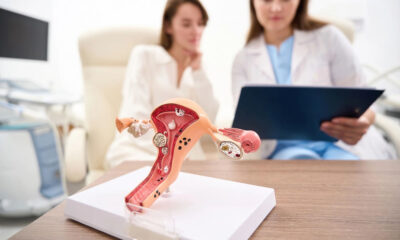

Rok po rewolucji: Jak powszechny dostęp do badań prenatalnych wpłynął na zdrowie i świadomość społeczeństwa w Polsce?
Wprowadzenie nowych zasad dotyczących badań prenatalnych w Polsce budzi wiele emocji. W ciągu pierwszego roku od ich wdrożenia zauważalny jest wyraźny wpływ na zdrowie...
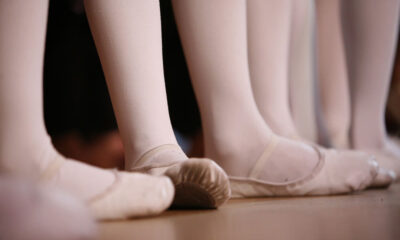

Sporty dla dziewczynek – które sprawdzają się najlepiej?
Wybór odpowiedniego sportu dla dziewczynki to jedna z najważniejszych decyzji, które mogą wpłynąć na jej całe życie. Aktywność fizyczna nie tylko kształtuje zdrowe nawyki, ale także...
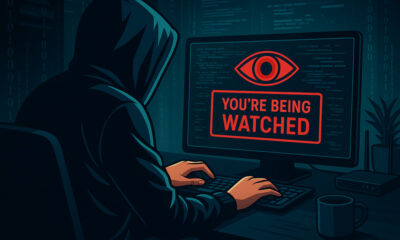

Jak sprawdzić, czy ktoś zdalnie obserwuje Twój ekran w komputerze?
W dobie powszechnych połączeń zdalnych, aplikacji do pracy online, zdalnej pomocy technicznej i komunikatorów, zdalny dostęp do ekranu komputera stał się czymś codziennym. Niestety,...
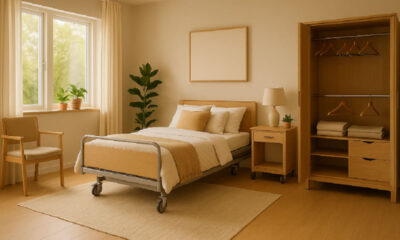

Czy łóżko rehabilitacyjne elektryczne zużywa dużo prądu?
Wielu opiekunów osób chorych, starszych lub z niepełnosprawnościami staje przed pytaniem: czy łóżko rehabilitacyjne elektryczne nie podniesie znacząco rachunków za prąd? W czasach rosnących cen energii...
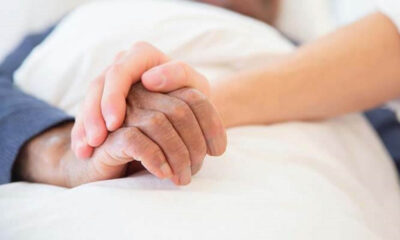

Jak zmienić pozycję chorego bez wysiłku fizycznego?
Zmienianie pozycji chorego w łóżku to codzienność setek tysięcy opiekunów w Polsce. Czasem robimy to intuicyjnie, czasem z trudem, obawiając się, że zrobimy krzywdę albo sobie, albo osobie,...
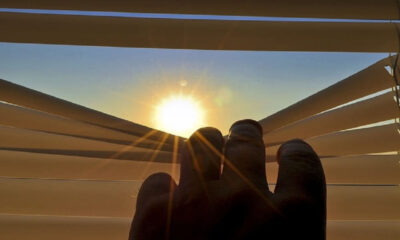

Jak dobrać rolety do aranżacji?
Wybór odpowiednich rolet to już nie tylko kwestia ochrony przed światłem i zapewnienia prywatności. W 2025 roku osłony okienne stają się istotnym elementem wystroju wnętrza, integrują...
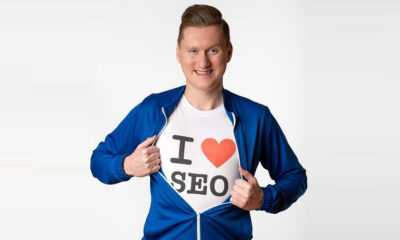

Co to jest audyt SEO i kiedy warto go wykonać?
W dobie cyfrowej transformacji, obecność firmy w wyszukiwarce Google to nie luksus, a konieczność. SEO, czyli optymalizacja stron internetowych pod kątem wyszukiwarek, pozwala osiągać lepszą widoczność...
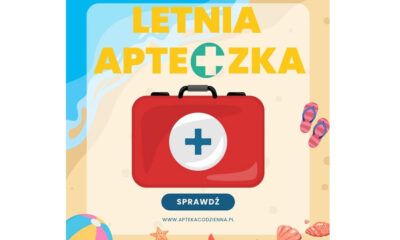

Domowa apteczka seniora — co powinno się w niej znaleźć?
Wraz z wiekiem zwiększa się ryzyko występowania różnych schorzeń, dlatego warto zadbać o to, aby domowa apteczka seniora była odpowiednio wyposażona. To nie tylko kwestia...
Popularne artykuły
-
Lifestyle2 tygodnie temu
Łóżko na pilota dla chorych – jak z niego korzystać?
-
Podróże2 tygodnie temu
Wyprawa terenówką po bezdrożach
-
Lifestyle2 tygodnie temu
Jak nauczyć dziecko zegara? 14 sprawdzonych metod
-
Lifestyle2 tygodnie temu
Jak dbać o higienę skóry osoby długotrwale leżącej?
-
Lifestyle2 tygodnie temu
Czy pilates może poprawić jakość snu?
-
Lifestyle2 tygodnie temu
Blachy stalowe niskostopowe – fakty i ciekawostki
-
Lifestyle2 tygodnie temu
Jak często ćwiczyć pilates, żeby zobaczyć efekty?
-
Lifestyle2 tygodnie temu
Jak przygotować się na pierwsze zajęcia pilates?
-
Podróże6 dni temu
Weekend w górach – dlaczego Karpacz to najlepszy wybór na krótki wypoczynek?